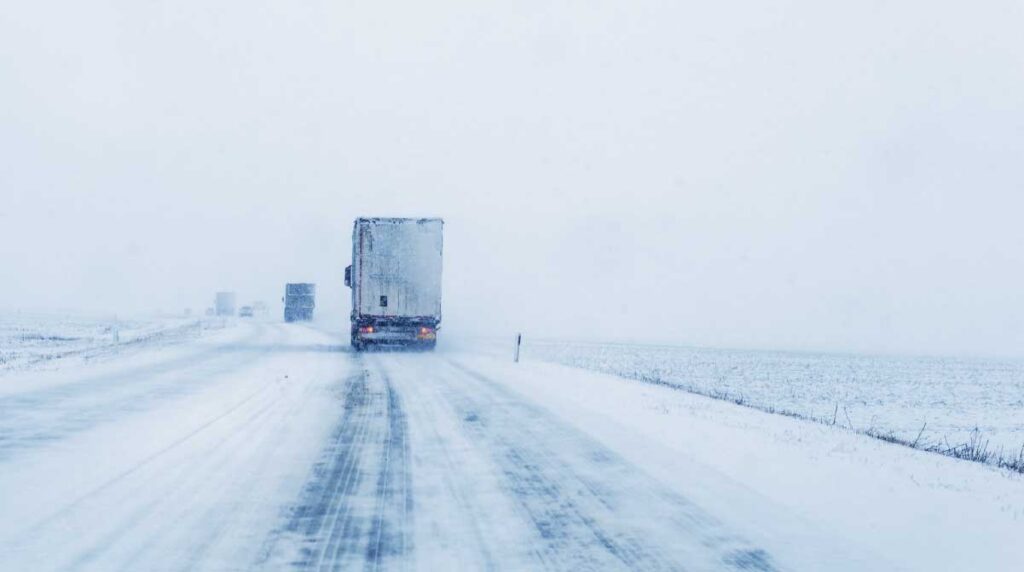
In the last three decades, globalization has made our lives so much more convenient. We have access to all kinds of resources at our disposal. Living in big cities, we still have access to the produce from far away farms. Cold chain logistics is that segment of the supply chain which makes this access possible. Transporting temperature-sensitive products from one place to another can be daunting with the constant risk of spoilage. As these items demand specific care and standards to stay in good condition for longer periods, cold chain logistics comes into play.
Dedicated storage, management, and transportation of products in cold temperatures to extend the shelf life all constitute cold chain logistics. Starting from basic food like vegetables, fruits, and dairy products to processed items and lifesaving medicines, all must be delivered to the point of consumption in extremely high quality. Effective logistics in the cold chain make sure that the product quality remains intact throughout the process.
What Is Cold Chain in Logistics?
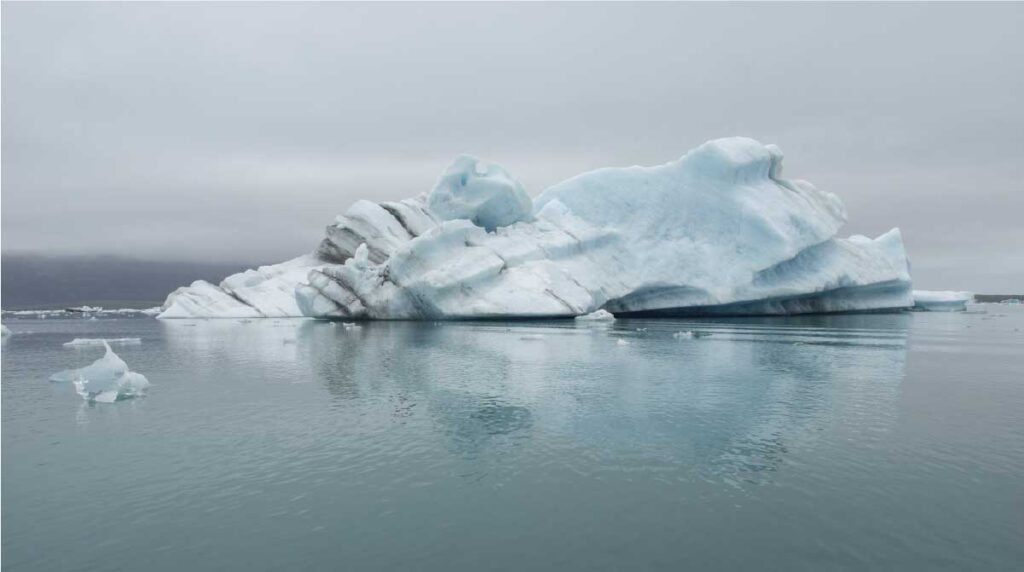
The term "cold chain" describes a temperature-controlled supply chain that aims to keep goods within a specific temperature range while they are being transported to preserve their integrity.
Logistics for the cold chain do not begin when a product is put on a vehicle, but each phase of the procurement and supply has to be constantly monitored as per the defined processes, including sourcing, shipping, warehousing, and last-mile delivery. Temperature-sensitive materials must be stored and transported at constant temperatures.
If the cargo is subjected to temperature changes throughout this procedure, it can be disastrous for the goods being transported. There are losses of commodities every year, particularly in the pharmaceutical industry, but there is also a lot of danger in the perishable industries. The proper packaging, the appropriate transport tools, carefully selected delivery routes, ideal timing, and excellent visibility from the point of purchase to the point of delivery all become extremely crucial in cold chain logistics with storage and transportation being the major segments of the market.
Indian Cold Chain Logistics Market Drivers
Growing with a CAGR of 15.1%, the global cold chain logistics market is poised to reach a valuation of $647.47 billion by 2028. Similarly, the market valuation of the Indian cold chain market in 2021 was INR 1585.1 billion which is expected to rise to 40.7 million metric tonns of total perishables by 2023.
Future trends in this sector may result in built-to-suit assets with custom specifications and diversity, catering to higher-value commodities using sustainable solutions for reducing operational costs
The expansion of global trade and supply chains is directly responsible for the rise in cold chain logistics demand. Today, any effective contemporary supply chain solution must include cold chain logistics. The major factors contributing to this growth rate are as followed.
- Growth in Organized Food Retail
- Growth in the Processed Food Sector
- Shift Towards Fruits and Vegetables
- Increasing Demand from the Healthcare Sector
Key Components for Successful Cold Chain Logistics Business

Having the right tools and strategies for complex requirements is very important for the success of a cold chain logistics business and capitalization on the increased demand.
Automation
Putting your entire cold chain logistics business on autopilot mode drives the operations while increasing your productivity. Delivering shipments is also a part of cold chain management. Automated delivery is dependent on the preferred means for receiving cold shipments from the end-user consumers. Automation of the processes decreases the probability of human error and gives you access to data so you can analyze the efficiency of your processes and make business decisions accordingly.
Packaging
To retain their quality, temperature-controlled products require suitable packaging. The risk of product contamination is decreased with proper packing, which also guarantees cold chain storage that uses as little energy as possible.
Phase change material (PCM), dry ice, gel packs, gel blocks, and EPS panels are the most popular refrigerants used in packaging (expanded polystyrene or Styrofoam).
Efficient Infrastructure
Having a state-of-the-art infrastructure is integral to establishing an efficient cold chain logistics business. The first step in the cold chain is the product's storage in a refrigerated location.
Refrigerated containers, cold rooms, chillers, cold boxes, blast freezers, etc. are examples of common cold storage equipment and facilities and increasing the shelf life, quality, and efficiency of a wide range of products.
Top Challenges of Cold Chain Logistics
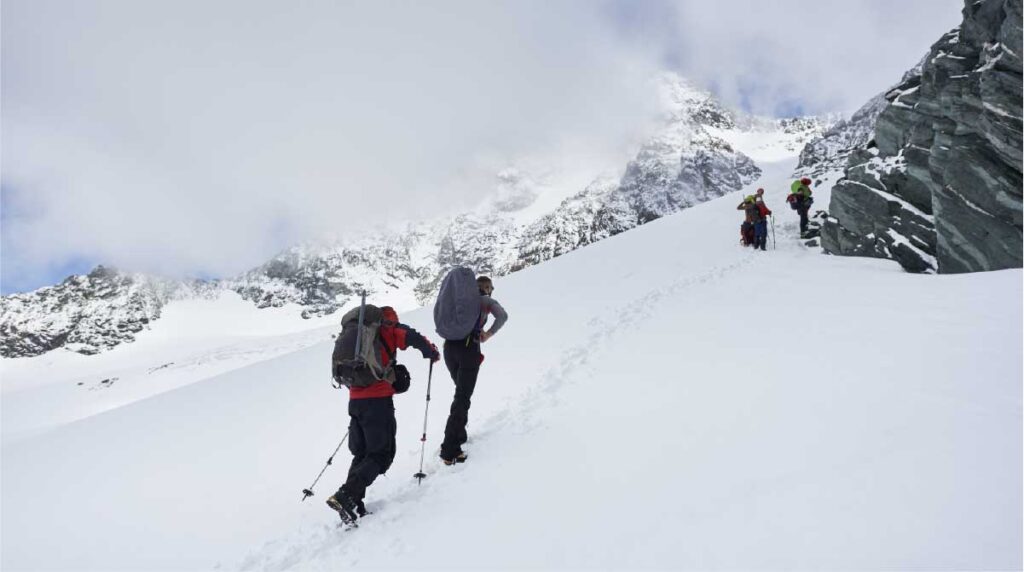
Supply chain risk management is a costly affair, and that’s especially true for a cold chain. Shippers are urged to expect the worst while being at their best when handling high-value shipments, ensuring there’s enough care and contingency in place to mitigate unexpected risks.
Nonetheless, it’s a necessary cost to avoid unnecessary loss, especially when you weigh the strategic importance of cold chains.
Supplier Risks
Bad quality raw materials and bad packaging practices are the major challenges for the chain. This issue is quite prominent when it comes down to loading and unloading goods. Just as any individual feels dehydrated after being in a heated environment, the goods degrade when exposed to heat for a long duration. These can be prevented by ensuring proper quality checks and following standard packaging processes while maintaining required temperatures at the origin of the shipment,
Distribution/Delivery Risk
The distribution process comprises transport and storage. While the storage is usually easier, temperature management in logistics and transportation isn’t as foolproof. Packaging Failure, Hardware Failure, Vehicle or Modal Breakdown, or simply lack of Equipment at any stage can disrupt the whole chain.
Human Error
While new cold chain technologies and techniques go a long way toward improving cold chain efficiency and security, they can all fail if the people handling your goods aren’t using them properly. The shipment’s life can dramatically reduce by bad handling including touching or leaving the product in the wrong temperatures for long times while transferring, pickup and delivering.
A cold chain isn’t about keeping things cold, it’s about temperature control. Fresh vegetables and fruits can be spoilt even in sub-zero temperatures if exposed for a long. They need to be transported in heated containers during winters, so they last longer. So, the Staff has to be well trained to understand the particular needs of the product being supplied.
Lack of Premeditation
The cold chain supply can be put at risk if the high risk of contamination is ignored while transportation. Route changes and continuous coolant supply have to be considered in case of any delays on roads. Similarly, while it is lucrative to save power and turn off the equipment at intervals, to maintain the quality of the chain it is essential to keep the storage units at defined temperatures before the shipment is arrived to avoid any fluctuations in temperature hampering the quality.
Methods To Prevent The Loss Of Product Quality In Cold Chain
Most of the challenges of the cold chain can be overcome by employing real-time cold chain monitoring systems which can monitor your temperature-controlled shipments in transit as well as in storage facilities.
Temperature data loggers only provide you with post-shipment audit trails, but with so many things that can go wrong for your cold chain supply, you need actionable real-time data at multiple stages.
But with real-time location tracking and condition monitoring solutions, you can track the shipment’s location to understand the condition so you can
- Estimate what might be going wrong if you have had incidents of quality changes,
- Analyze patterns and predict if something is going to go wrong in the future and
- Take preventive measures promptly with better control and initiate corrective action before the shipment is destroyed,
- Monitor details in addition to temperatures, such as humidity which is critical for certain types of vaccines and perishables, while considering the details for Safety (to recall compromised products before they hit the customer causing damage) and financial aspects (such as whether to recall only the product in transit or rather the complete batch).
Best Practices To Successfully Manage Your Cold Chain Supply
Choose the correct processes and packaging for your product- Reduce human touch and automate as much as possible. Keep the warehouse decontaminated and equipment well serviced.
Regulate the temperatures throughout the process – Atmosphere control is the most essential part of the chain to prevent spoilage and contamination. Minimize the time spent in handling, loading, and unloading to maintain the shipment’s integrity.
Track the resources in real-time to ensure the safety of the shipment and timely delivery while minimizing loss. Tracking can also help in streamlining your processes by analyzing the pain points, so the cold chain reaches maximum efficiency.